Laser Scanning - SICK LMS500,LMS511 - 20
Description
Driver to decode laser data from SICK LMS5xx laser scanners, through an Ethernet interface.
Laser stands for L ight A mplification by S timulated E mission of R adiation. Laser class used by the LMS5xx is 1 (IEC 60825-1 (2007-6)), which is eye-safe.
The scanner has a maximum scan range of 65 meters (newer scanners may scan 80 meters), and its full scan area covers 190°. The driver supports the so-called multi-echo technology, which means that each emitted pulse may provide up to five measurements, depending on the environmental conditions (rain, dust, etc.). The remission value (signal strength or reflectivity) for each pulse is also decoded.
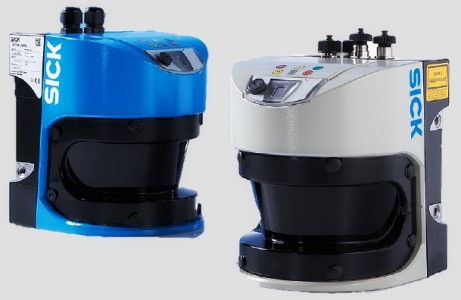
On the left the LMS500 for using indoors, on the right the LMS511, which can be used outdoors (IP 67).
New
This driver supports the SICK LMS5xx since mid June 2011.
The newer SICK LMS511 PRO is supported since October 2013.
Driver Information
Driver | SICK LMS500/LMS511 (XML) | Interface Type | TCP/IP | Driver Class Type | Freebase/TCP |
---|---|---|---|---|---|
Yes | Input / Output | Input/Output | Executable | DrvLaser.exe SICK_LMS500 | |
Related Systems |
| ||||
Related Pages |
Decoding Notes
Data is always broadcast via TCP network. It is advisable to use a fast (at least 100Mbit) network card, due to real-time scanning and the huge amount of data. Communication via the USB or serial interface is not supported.
The actual raw datastream is in SICK's own format. This document does not describe this format.
Interfacing Notes
Timing
An LMS5xx unit does not support accurate timing by means of an external synchronization pulse (PPS), nor has it an accurate real-time clock inside.
Therefore the driver will time-stamp by default the data when received at the TCP port. This time-stamp may be corrected for a fixed latency, which can be provided by the manufacturer, or established by a latency calibration procedure.
It is however possible to synchronize the scanner with an external time and date stamp using the serial data link of the scanner. Outputted data will then contain time of transmission for each laser echo. The user is allowed to use this one for time-stamping the data, and therefore eliminating a possible jitter or variable latency d/t the TCP connection. A valid PPS system must be part of the template setup.
Network setup
All communication to and from the laser unit goes via the on-board LAN network, using the TCP protocol.
The exact LAN IP address of the laser unit should be provided by the manufacturer or your reseller. Normally SICK configure their laser units with IP address 192.168.0.1. The default TCP port number is 2111. See paragraph SOPAS settings below for more information about how to establish the exact IP address and port number.
The LAN IP address of your computer's network should be in the same range, except for the last digit. This must be a unique number! Use for the subnet mask the values 255.255.255.0
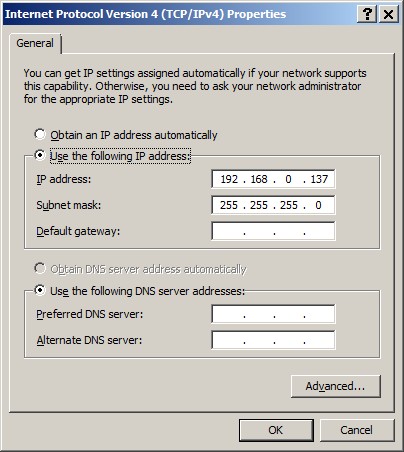
Windows XP:
Control Panel, Network Connections, Click right-mouse on Local Area Connection, Properties, Internet Protocol (TCP/IP), Properties...Windows Vista:
Control Panel, Network and Sharing Center, Tasks, Manage network connections, Click right-mouse on Local Area Connection, Properties, Internet Protocol Version 4 (TCP/IPv4), Properties...Windows 7:
Control Panel, Network and Sharing Center, Change adapter settings, Click right-mouse on Local Area Connection, Properties, Internet Protocol Version 4 (TCP/IPv4), Properties...
It is recommended to check the network connection between your computer and the laser unit, before commencing any scan operation. You may do this by using the ping command from the Windows Command Prompt:
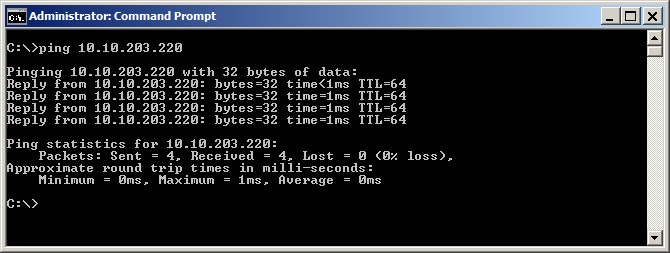
Select Start from the Windows Taskbar, Run..., Cmd <Enter>, and 'ping' the IP address of your laser unit.
The network connection is okay when you receive a reply three times within a few milliseconds.
System Configuration
Use the official SICK SOPAS software to initialize the scanner with some necessary settings in order to operate it from Qinsy.
Select Start, Programs, SICK, SOPAS Engineering Tool, SOPAS...
During start-up the program will scan automatically for any connected SICK device. If no results are displayed, check the network and/or power cable of the scanner. You may have to turn off your WiFi network in order to let the program find a device.
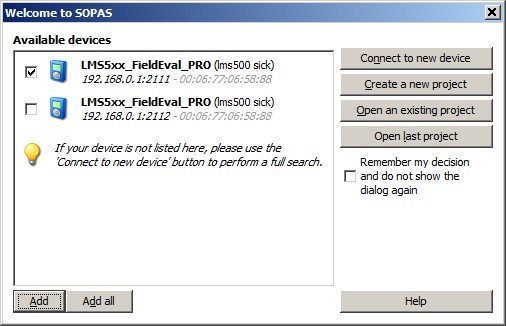
Enable the one found at port 2111 and select the Add button in order to continue.
The Data processing settings are the most important ones to check:
Remission, Encoder data and Time stamp must be enabled.
The Device name must be disabled and the Output interval must be 1.
The Output data range Start angle must be the minimum allowed -5° and the Stop angle must be the maximum allowed 185°.
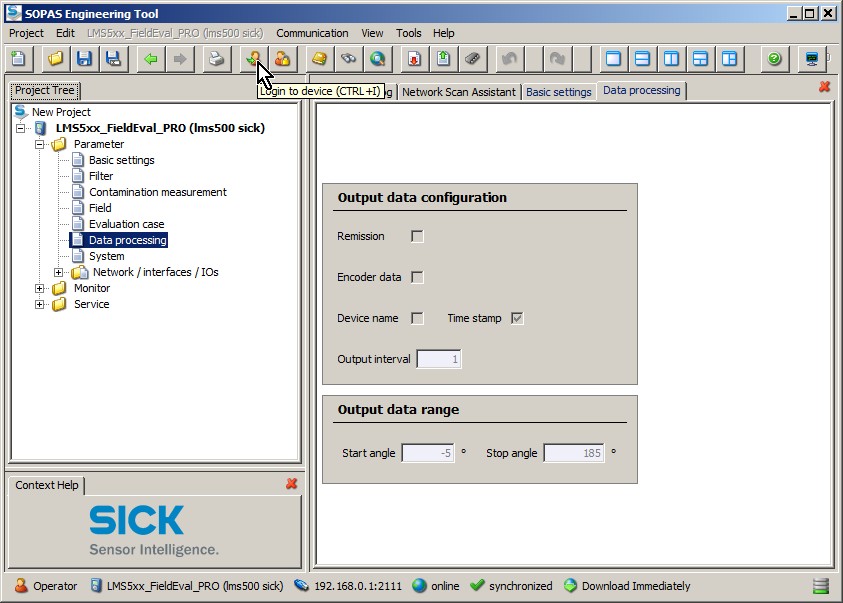
In order to change these settings you need to login first. Select Login device from the Tools pull-down menu:
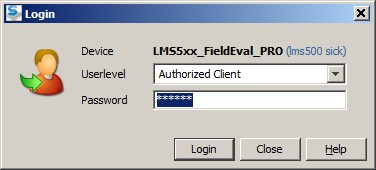
Set Userlevel to Authorized Client and login using password: client .
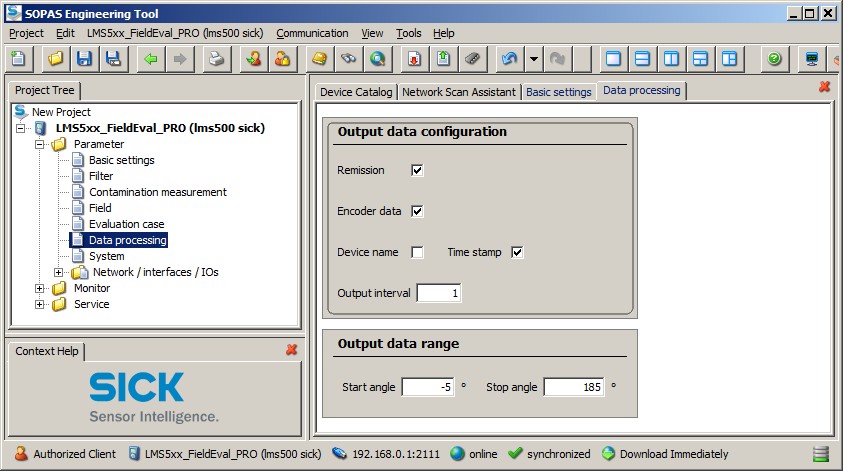
After changing the parameters select from the Communication pull-down menu the option Download all parameters to device.
Further, double click on the Ethernet settings in the tree to check the IP address and Ethernet aux port (default 2111) which is needed to enter in the Qinsy template setup for the Laser system.
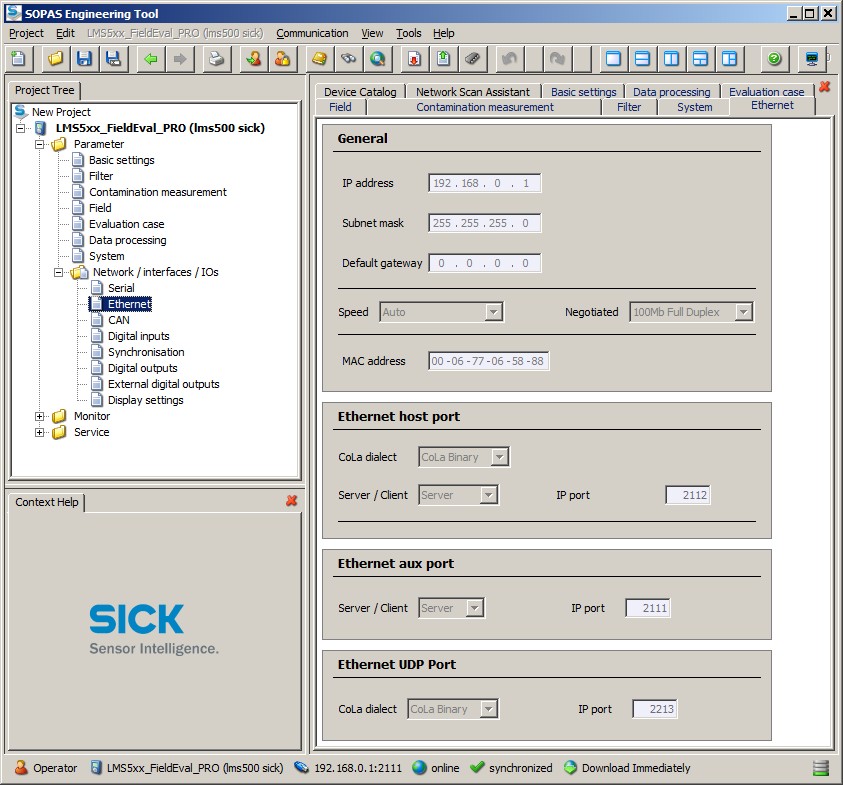
In case you want to synchronize the time externally by using a serial data cable connected between your PC COMport and the IO Data link, double click on the Serial settings in order to check the required baud-rate settings. Default these will be 57600, 8, 1, none.
Database Setup
The driver is internally treated as a multibeam system, creating multibeam 'range' and 'angle' observations, therefore you will find the laser system drivers under category type Multibeam Echosounders.
Terminology 'Multibeam' versus 'Laser scanning'
Multibeam | Laser scanning |
---|---|
Ping | Scan (i.e. full 190°) |
Footprint or Beam | Pixel, Pulse or Echo |
Swath | Line or Scan |
1. Edit System Wizard
Add a Multibeam Echosounder system to your template setup, and select driver "Laser Scanning - SICK LMS500/LMS511 (XML)".
The Port number must be the same as the configuration port of the scanner. The driver will communicate via this configuration port of the scanner. Ask the manufacturer or reseller what the exact port number should be. Normally it will be 2111.
Also important is to enter the exact IP Address of the scanner. Each scanner should have its own unique IP address. See Network Setup for more information.
Leave the maximum update rate at zero.
2. Multibeam Echosounder Parameters
Important are the Transducer Location (Node) and Mounting Angles (offsets) on the second wizard page.
As a rule of thumb, when you mount the laser unit backwards on your moving vehicle (connectors and cables pointing to bow), and the face (scan area) of the unit is pointing downwards, then you may leave the Roll, the Pitch and the Heading offset zero. A scanned profile as seen in a Raw Multibeam display should then be as in the real world.
As another example, if you mount the scanner backwards, but with the face pointing to port, then you should enter already a Roll offset of 90°. When the face is pointing to starboard, use a Roll offset of 270°.
Leave the Max. beams per ping value to 5706.
The actual number of beams will be variable, and depends for example on the used on-line settings and on the targets being scanned.
3. Echosounder Accuracy Parameters
You may leave all values on the third wizard page at defaults.
4. Multibeam Echosounder Corrections
You may leave all values on the last wizard page at defaults.
Online
When on-line, the laser unit can be controlled using the Controller:
Select Echosounder Settings, click on the Laser System icon, and select the 'Control' tab page.
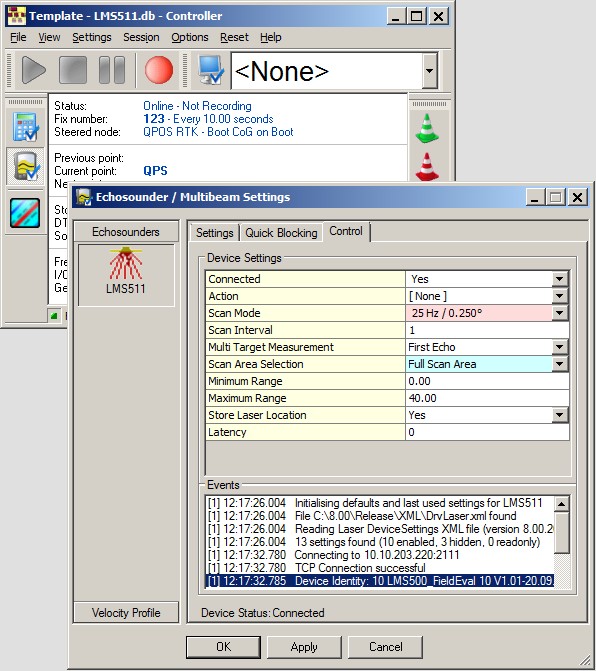
Control | Device Settings |
---|---|
Connected | In order to communicate with the scanner, you must make a network connection first.
|
Action | Selected action will be sent to the laser unit, immediately after hitting the Apply or OK button. You must be connected first in order to select an action.
|
Scan Mode | Select the required combination of Scan Rate and Angular Resolution. |
Scan Interval | Leave this value to 1, in order to receive all scans that belongs to the selected scan rate. However if you wish to decrease the predefined scan rate, you may want to set a value in order to use every nth scan. |
Multi Target Measurement | One single emitted pulse may produce several echoes, due to hitting a rain drop, a sand dust particle, glass, the edge of a tree leaf, etc.
The index of the echo is stored as Quality value for each laser pulse. This means that the quality for a first echo will be 1, the 2nd echo will be 2, and so on. So if you color-code the point cloud data using the Quality you should use a color range scale between 1 and 5. |
Scan Area Selection | The maximum physical scan area covers 190°, and it goes counter-clockwise from 95° to 265°.
|
Minimum Range | Set the minimum required range in meters. Valid values: 0 to 65 meters. |
Maximum Range | Set the maximum allowed range in meters. Valid values: 0 to 65 meters. |
Minimum Intensity | Set the minimum required intensity (RSSI or signal strength). Valid values: 0 to 255. |
Maximum Intensity | Set the maximum allowed intensity (RSSI signal strength). Valid values: 0 to 255. |
Store Laser Location | If enabled, an additional pixel with zero range will be added to each line scan, in order to indicate the exact laser scanner location in the resulting point cloud. This extra pixel will always have beam number 0, and its intensity and quality value will be zero. |
Use Time from Scanner | It is recommended not to use the time of the scanner, but to use the time of arrival. A valid PPS system must be part of the template setup, otherwise time of arrival will be used for time-stamping. |
Latency | Enter a fixed latency value in milliseconds. The time will be corrected by subtracting this value. |
Synchronize Scanner Time | This option is only visible in combination with the 'Use Time from Scanner' enabled. |
Capture Raw Data | Enable this option if you want to store the raw binary data stream coming straight from the unit to a log file on disk. |
Generic Display
The Generic Display can be used to show the numerical values for the number of beams (pixels) being scanned per ping (scan), the number of beams being scanned per second, the ping rate (scan rate in Hz), range values, etc.
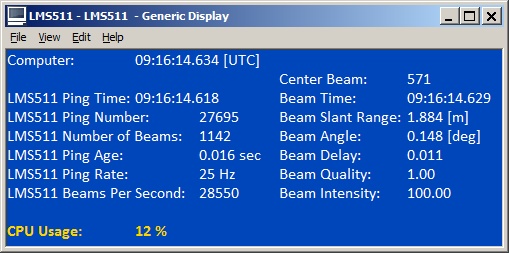
Important value to monitor is the Ping Age, especially when setting 'Use Time from Scanner' is enabled. This value should be small, around zero.
A Status Flag value of 2 means that the time from the scanner is used. If not, it will be 0.
You may use the attached example Generic Display Layout file as example: Copy this layout (Use 'Save Link As...') to your current Project's Settings\Display folder and open it using a new Generic Display. You only have to select the correct laser system as defined in your template setup.
Additional Information
The LMS5xx has the following features and limitations:
The maximum scanning range is 65 meters (213 feet) or 80 meters (262 feet) which depends on the selected angular resolution. The accuracy may depend on your exact scanner type.
The maximum scan area covers 190° (clockwise from 265° via 0° to 95°)
The highest angle resolution will be 0.1667°, the lowest is 1.0°
The decoded remission (intensity/reflectivity) value is a value between 0 and 255, and depends on the target's surface being hit, and the distance to this target. I.e. that a white surface will return a higher remission value than a dark surface. Also, a surface closer by will return a higher remission than the same surface at larger distance. This remission is also stored as intensity value for each laser pulse. So if you color-code the point cloud data using the Intensity you should use a color range scale between 0 and 255.
The number of scans per second can be 25, 35, 50, 75 or 100 Hz. (user-defineable)
Not all combinations between an angle resolution and scans per second are allowed. This driver only allows you to select valid combinations.The maximum expected number of beams (pixels) per second is 28500 (theoretically).
The actual number of beams depends on the on-line used settings, like scan mode, scan interval, scan area and/or the multi-target measurement selection. See Online Setup for more information.
If you experience problems using your laser scanner in combination with this driver or if you need additional information or support then please attach the daily laser log-file when submitting your JIRA support ticket.
At the bottom of this section you'll find the information on where to find this daily laser log file
Network Problems
Windows Firewall
A commonly reported problem is that network data is blocked by the Windows Firewall.
When this happens you may see that data does come in using other utilities (like the I/O Tester or the manufacturer's own software), but that the Qinsy driver does not accept any data.
The following (Windows 10) steps may solve this:
Go offline, open the PC Settings (Start menu, Settings)
Select Windows Firewall (Update & Security, Windows Security, Firewall & network protection)
Select Advanced settings
Select Inbound Rules, highlight all 'Driver for Laser Scanning' entries and delete them using the right mouse popup menu (or Del key)
If you now go online, the Windows Security Alert message will pop up: It is important to tick all three check boxes!
Multiple Network Cards
Another possible problem could be that your computer has more than one network card installed (e.g. LAN and WIFI), but within the same sub-net mask range (255.255.255.0).
It is recommended to make the first three digits unique for each network card IP address.
You may check the daily laser log-file; it will show the IP addresses for all available network adapters and indicates which one the driver will use:
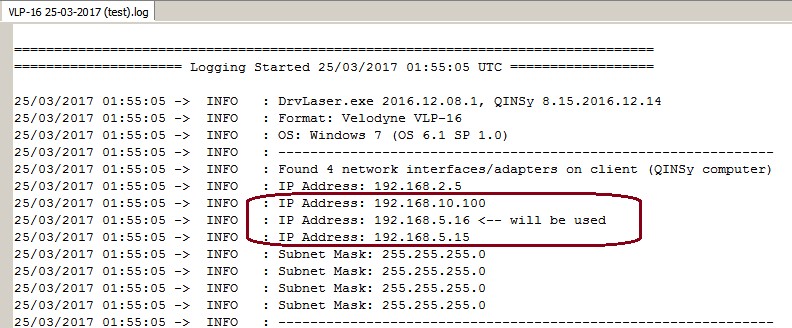
Please check that the driver is using the correct one!
Missing Data
If you occasionally experience gaps in your data, this may be caused by a general Windows setting that affects the data throughput of your network card.
Change the following registry key: HKEY_LOCAL_MACHINE\SOFTWARE\Microsoft\Windows NT\CurrentVersion\Multimedia\SystemProfile\NetworkThrottlingIndex
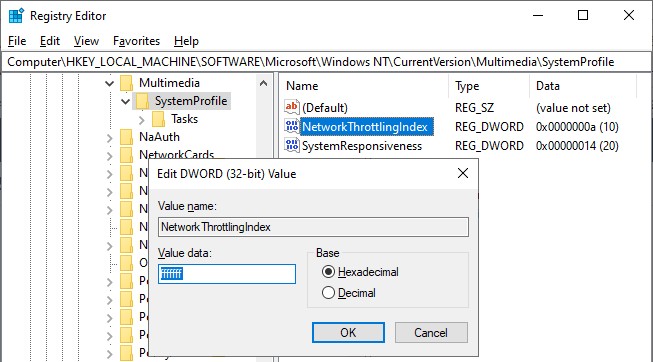
Set the new value to ffffffff (which will tell Windows to disable network throttling) and restart the computer.
Note that disabling network throttling may affect playing multimedia on your computer, but for laser scanning operations it is advisable to have a maximum data throughput of your network.
Daily Laser Log File
All user actions, system information and reported errors are logged in a daily laser log file which can be found in the current project's LogFiles subfolder.
The filename convention for this ASCII log-file is <System Name> DD-MM-YYYY.log, so every day there will be a new one.
Note that all time stamps in this log file are by default in UTC. An advanced user may change this to local time zone (LTZ) by changing the registry key:
HKEY_CURRENT_USER\Software\QPS\QINSy\8.0\Drivers\DrvLaser\Settings\TimeLogFileUtc value from 1 to 0.
Improve Performance
Due to the enormous amount of data to be expected while scanning and recording, it is recommended to keep the system overhead as low as possible.
Here you'll find some tips and tricks in order to fine-tune your setup.
However, these are not strict rules, because each project is different and depends on the current situation and hardware being used. Your goal should be to keep your system CPU usage as low as possible.
HARDWARE
Storage
Make use of Solid State Drive (SSD), or fast SATA hard drive (7200 - 10000 rpm).
Network
Your network card speed should never be lower than the scanner's network speed. Use a network card that can be configured for 100Mbit or 1Gbit speed. Do not use USB Networking Adapters, because this may result in loss of data when huge amounts of data are being broadcast.
Virus Scanner
Disable Virus Scanner or at least the setting 'Scan Files when Writing/Reading to/from disk'.
Task Manager CPU
General Task Manager CPU Usage should be less than 50%. CPU load of each display must be less than 10-15%.
Make sure that the 'Working Set (Memory)' column for process Multibeamer.exe and/or DrvResultOut.exe is not constantly increasing, especially during recording. For detailed information about this see the section Real-time Performance Monitoring below.
PROJECT PREPARATION
Controller Laser Device Settings
During project preparation, establish the optimum settings in order to achieve the required results.
The most benefit you will gain from setting the Min/Max Range limits, Scan Speed, Scan Rate, Scan Resolution, Angle Resolution, Vertical Area Selection, Scan Area Selection and Sector Reduction as well as possible.
Especially the Vertical or Scan Area Selection is very important. Make use of Mask schemes to define areas which you don't want to scan.
ONLINE
Raw Multibeam Display
Open only one Raw Multibeam Display and more important: do not use the options 'Show Big Dots' or 'Draw Lines'.
Navigation Display
Open only one Navigation Display.
Preferably disable DXF and TIFF layers or other big background files. Note that these layers should only be used during project preparation.
When 'object tracking' is enabled, do not zoom in too close. Keep in mind that the display should not be 'refreshed' more than 1x per second.
3D Point Cloud Display
It is not recommended to use a 3D Point Cloud Display, unless your hardware contains a high-spec video card.
Under Sensor settings set the Time window setting to a short period, e.g. 10 sec
Sounding Grid / Dynamic Surface
Storage to a grid is not recommended and should be purely for display purposes: e.g. for checking the scan coverage or for showing the 95% Confidence Level statistics.
If you do want to see the scan coverage then it is advisable to store to a sounding grid and not to the dynamic surface
Do not use a small cell-size; preferably not less than 1.0 meter.
If you notice in the Navigation Display that the real-time sounding grid is updated with a delay then please increase the cell-size or disable the storage completely.
Note that in Replay (offline) there are no limitations and you may use small cell-sizes, e.g. 0.10 meter.
OFFLINE
Replay
In Replay there are no limitations as mentioned above: use as many displays as you like, store to sounding grids with small cell-sizes, update the dynamic surface, etc.
All this may only affect the replay speed, but the data integrity of your final DTM processing files should be fine.
COMPUTATION SETUP
While working online, disabling the laser system in your Computation Setup will have the most effect on the performance
The final footprints will not be geo-referenced, nor corrected for motion, heading or timing in real-time, which will save a tremendous amount of CPU power and memory usage.
This tip allows you to get the most out of your scanner: maximum scanning speed and maximum scanning rate, without the risk of losing scans due to performance issues.
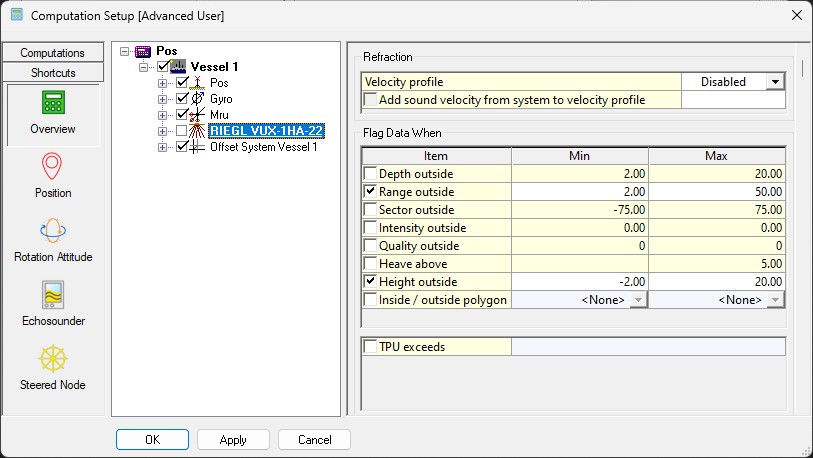
Drawback is that no DTM file (e.g. QPD) is created, nor a sounding grid is filled, while working online.
In order to create a final DTM and/or Sounding Grid file you just need to Replay the recorded databases afterwards.